Explosion-protected devices
Summary
An explosion-protected device is certified for use in hazardous areas where flammable material (liquid, gas, vapor, or dust) may be present. Areas classified as hazardous are often found in industrial operations like oil and gas extraction, transportation, and refining; chemical plants, underground mining, saw mills, and food processing, where the use of surveillance cameras can significantly improve health and safety, operational efficiency, and security.
Electrical installations in hazardous areas are subject to rigorous requirements, and compliance is verified through testing to industry standards. All standards are based on the same criteria, mainly concerning the type of flammable gas or dust that may be present, its possible concentration, and duration.
There are three certification schemes used in different parts of the world:
The IEC Zone system is used worldwide and is described in the IEC 60079 set of standards for the IECEx certification or national deviations of these standards.
The Class/Division system is primarily used in North America. It is described in the National Electrical Code (NEC).
The Class/Zone system is also used in North America and described in the National Electrical Code (NEC).
Products that are certified for use in hazardous areas must be labeled to show the type and level of protection applied, as well as details about the certification.
Axis designs explosion-protected devices that use the explosion protection principles of containment and prevention:
The devices that are certified for use in Zone/Division 1 hazardous areas have heavy-duty enclosures that confine the energy. In case of explosion caused by sparks or high temperatures in these devices, the explosion will be limited to within the enclosure and not spread to the flammable atmosphere outside of it. These devices can be used also in Zone/Division 2 hazardous areas.
The devices that are certified for use in Zone/Division 2 hazardous areas instead use the prevention principle. By design, these devices can’t provide sufficient energy to ignite the gas or dust and no explosion can occur.
In hazardous locations, Zone/Division 2 areas are typically much more common than Zone/Division 1 areas and cover a larger percentage of the hazardous area. Devices certified for Zone/Division 1 areas can also be used in Zone/Division 2 areas, but Axis devices specifically designed and certified for Zone/Division 2 areas are a more cost-efficient alternative.
Introduction
In hazardous areas, strict rules apply regarding which type of equipment is allowed. Explosion-protected devices are typically used for HSE (health, safety, environment) applications and process monitoring.
This white paper covers the basics of explosion and explosion protection. It also outlines the applicable industry standards, certifications, and product marking systems in place for electrical equipment in hazardous environments.
Basics of explosion
An explosion is a rapid process that releases energy and gives rise to a shock wave. For an explosion to occur, three components must be present: fuel, oxygen, and energy. If one or more of these components is removed, no explosion will take place.
An explosive atmosphere is defined as a mixture of air and flammable substances in the form of gases, vapors, dusts, or fibers, under atmospheric conditions. Energy is required to ignite the combustible mixture, and after ignition the combustion spreads to the entire unburned mixture.
The source of an ignition can be lightning strikes, open flames, mechanically generated impact or friction sparks, electric sparks, radiation, electrostatic discharge, high surface temperature, or shock waves. An area where there is a risk for explosions is called a hazardous area.
- Energy — ignition caused by, for example, electric sparks or high surface temperature in an electric device.
- Oxygen — naturally prevalent in most environments.
- Fuel — flammable substances, such as gases, vapors, dusts, or fibers.
Combustible dusts and fibers
A material can only burn at its surface, where it reacts with oxygen. Dusts and fibers have large surface areas compared to their masses, which makes material in dust or fiber form much more flammable than the same material in a bulk form. Because the particles are very small, they need much less energy to catch fire than the bulk material, since no energy is lost through thermal conduction within the material. Coal, sawdust, aluminum dust, starch, pollen, sugar, and flour are examples of combustible dusts. In regulations, they may be classified by whether they are conductive or non-conductive, and by the size of the particles. Cotton, rayon, and hemp are examples of combustible fibers.
Combustible gases
Combustible gases normally require very little energy to react with naturally prevalent oxygen. They are often compounds of hydrogen and carbon.
Hazardous areas
A hazardous area is an area where flammable liquids, vapors, gases, or combustible dusts and fibers are likely to occur in quantities sufficient to cause a fire or explosion. Such areas include oil refineries, rigs and processing plants, gas pipelines, automotive and aircraft refueling stations, but also sewerage treatment plants, woodworking areas, and places where grain is handled and stored.
Other names for hazardous areas are Ex areas, classified areas, explosive areas, or hazardous locations, also known as HAZLOCs.
Safe areas
Explosion-protected devices are designed for use in hazardous areas. In non-hazardous areas, also called safe areas, Axis standard product portfolio can be used. This comprises a wide range of versatile, high-quality cameras, video analytics applications, physical access control products, and network audio products for normal and harsh environments.
Principles of explosion protection
Electrical equipment used in hazardous areas must be designed to be explosion protected. There are three basic principles for explosion protection:
Containment — if an explosion should occur it will be confined to a well-defined area and prevented from propagating to the surrounding atmosphere. Flameproof or explosion-protected enclosures take advantage of this principle.
Prevention — the electrical and thermal energy is limited to safe levels, both during normal operation and if a fault should occur. Equipment that is intrinsically safe and equipment with increased safety use this principle.
Segregation — electrical parts or hot surfaces are physically separated from the explosive atmosphere. Segregation can be accomplished by various techniques, such as pressurization and encapsulation.
Types of protection
The table lists the types of protection that can be used in different zones and divisions according to the industry standards, and which principle of explosion protection they employ.
Designation | Type of protection | Zone | Division | Principle |
---|---|---|---|---|
Ex d | Flameproof (explosion-protected) enclosure | 1, 2 | 1, 2 | Containment |
Ex e | Increased safety, non-incendive | (1)(1), 2 | 2 | Prevention |
Ex I | Intrinsically safe | 0, 1, 2, 20, 21, 22 | 1, 2 | Prevention |
Ex o | Oil immersion | 1, 2 | 1, 2 | Segregation |
Ex p | Pressurized (purged) apparatus | 1, 2, 21, 22 | 1, 2 | Segregation |
Ex q | Powder (sand) filling | 1, 2 | 1, 2 | Segregation |
Ex m | Encapsulation | 0, 1, 2, 20, 21, 22 | 1, 2 | Segregation |
Ex n | Non-incendive and/or normally no sparking circuits | 2 | 2 | Prevention |
Ex t | Dustproof enclosure | 20, 21, 22 | 1, 2 | Containment and segregation |
- Products in the category Ex e can be used in Zone 1 if they don’t contain semiconductors or electrolytical capacitors.
Axis explosion-protected cameras and speakers belong to the protection category Ex d, Ex e, or Ex t. For equipment designated Ex d, an explosion-protected housing should prevent any potential flame propagation from an internal explosion spreading to the surrounding gas mixture. Ex e, increased safety, is an explosion protection method for gas and dust environments that prohibits arcs, sparks, or hot surfaces. Ex t is an explosion protection method where the enclosure restricts the surface temperature and keeps ignitable dust out from the electronics.
Temperature classes
A mixture of air and hazardous gases may ignite by coming in contact with a hot surface. Whether an ignition will occur depends on the temperature of the surface area and the concentration of the gas. The ignition temperature, or auto-ignition temperature (AIT), is the lowest temperature of a substance, whether solid, liquid, or gaseous, to initiate a self-sustaining combustion. Apparatus used in any hazardous area must not have any surface whose temperature exceeds the AIT, neither during normal nor abnormal operation.
The maximum temperature of a piece of equipment must always be lower than the AIT of the gas, vapor, or air mixture in which it is placed. Certified equipment is tested for maximum temperature ratings by approval agencies. Tested equipment receives a temperature code indicating the maximum surface temperature.
Temperature code Zone 0, 1, and 2 | Temperature code Division 1 and 2 | Permissible surface temperature of electrical equipment |
---|---|---|
T1 | T1 | 450 °C (842 °F) |
T2 | T2 | 300 °C (572 °F) |
T2A | 280 °C (536 °F) | |
T2B | 260 °C (500 °F) | |
T2C | 230 °C (446 °F) | |
T2D | 215 °C (419 °F) | |
T3 | T3 | 200 °C (392 °F) |
T3A | 180 °C (356 °F) | |
T3B | 165 °C (329 °F) | |
T3C | 160 °C (320 °F) | |
T4 | T4 | 135 °C (275 °F) |
T4A | 120 °C (248 °F) | |
T5 | T5 | 100 °C (212 °F) |
T6 | T6 | 85 °C (185 °F) |
Note that the ambient temperature also affects which temperature code is applicable. For example, if the product by itself generates 10 °C (or, for example, 10 °F), but is used in an ambient temperature of maximum 80 °C (or 180 °F), the maximum surface temperature will be 90 °C (or 190 °F), and the product must be classified as T5. Products that are classified as T6 are allowed for use in areas that require T5-classified equipment, and so on, while T5 equipment can’t be used in areas that require T6-classified products.
Area classification
Area classification is a method of analyzing and classifying the environment where explosive gas atmospheres may occur, so as to facilitate the proper selection, installation, and operation of electrical equipment to be used safely in that environment. The classification also takes into account the ignition characteristics of the gas or vapor, such as ignition energy and ignition temperature. It is also used to give an assessment of the likelihood of an explosive dust atmosphere occurring.
The procedure for identifying combustible dust zones is as follows:
Identify whether the material is combustible and, for the purpose of assessment of ignition sources, determine the material characteristics. Parameters such as particle size, moisture content, cloud and layer minimum ignition temperature and electrical resistivity shall be considered. The appropriate dust group, Group IIIA for combustible flyings, Group IIIB for non-conductive dust, or Group IIIC for conductive dust, shall be identified.
Identify items of equipment where explosive dust mixtures may be contained or sources of dust release can be present.
Determine the likelihood that dust will be released from those sources and thus, the likelihood of explosive dust atmospheres in various parts of the installation. Wind direction, distance to the sources, and other aspects related to the surroundings should also be factored in.
After these steps have been taken, zones can be identified and their boundaries defined in line with the Zone system specified in the next chapter.
A corresponding procedure can be followed for identifying combustible gas zones.
A similar approach is also used when classifying divisions according to the Class/Division system used in North America.
Industry standards and certification
Electrical installations in hazardous areas are subject to rigorous requirements, both on equipment and on the competence of the installer. Compliance to the requirements is verified through testing to various industry standards.
Besides the electrical equipment, cable glands, thread adapters, and blanking plugs must be certified for hazardous areas. Cables must be suitable for use in the area according to local regulations, which may incorporate requirements regarding the type and thickness of the cable and how it is protected.
For classification and certification of explosion-protected equipment, the different standards are based on the same criteria. They mainly concern whether an explosive atmosphere will be caused by gas or by dust (or both), what the concentration is of gas and/or dust, and the duration of this concentration.
There are three different certification schemes used in different parts of the world. They are the IEC Zone system used worldwide, the Class/Division system primarily used in North America, and the hybrid Class/Zone system also used in North America. Local variations and exceptions to the Zone system may apply, for example ATEX, EAC, or INMETRO.
The IEC Zone system
The International Electrotechnical Commission (IEC) issues the IEC 60079 set of standards about electrical equipment in explosive atmospheres. National deviations of these standards are used throughout the world.
In the European Union, equipment must comply with the essential requirements of EU Directive 2014/34/EU, also known as the ATEX Directive, describing what equipment and work environment is allowed in an area with an explosive atmosphere.
The voluntary IECEx Equipment Certification Scheme can facilitate acceptance of equipment for use in an explosive atmosphere in other major jurisdictions around the world. IECEx is IEC’s system for certification to standards relating to equipment for use in explosive atmospheres.
Zones
Hazardous areas are divided into zones. The zone is defined by the probability that hazardous material will be present in an ignitable concentration in the surrounding atmosphere.
Zone | Hours per year of flammable gas-air mixture or dust clouds present | |
---|---|---|
Gas | Dust | |
0 | 20 | 1000 or more hours/year (10%) |
1 | 21 | 10 < hours/year < 1000 (0.1% - 10%) |
2 | 22 | 1 < hours/year < 10 (0.01% - 0.1%) |
For gases, Zone 0 is an area in which an explosive gas-air mixture is continuously or frequently present, or present for lengthy periods. Zone 1 is an area in which an explosive gas-air mixture is likely to occur for short periods during normal operation. In Zone 2, an explosive gas-air mixture is not likely to occur. If it does occur, it will exist due to abnormal conditions and for a very short time.
For clouds of combustible or conductive dusts, the equivalent zones are 20, 21, and 22.
Zones 1 and 2 (or 21 and 22 for dust) are the most common classifications, whereas Zone 0 (or 20 for dust) is restricted to small, inaccessible areas or areas inside technical equipment. Products certified for Zone 0 (20) can be used in Zones 0, 1, and 2 (20, 21, and 22). Zone 1-certified (21) products can be used in Zones 1 and 2 (21 and 22).
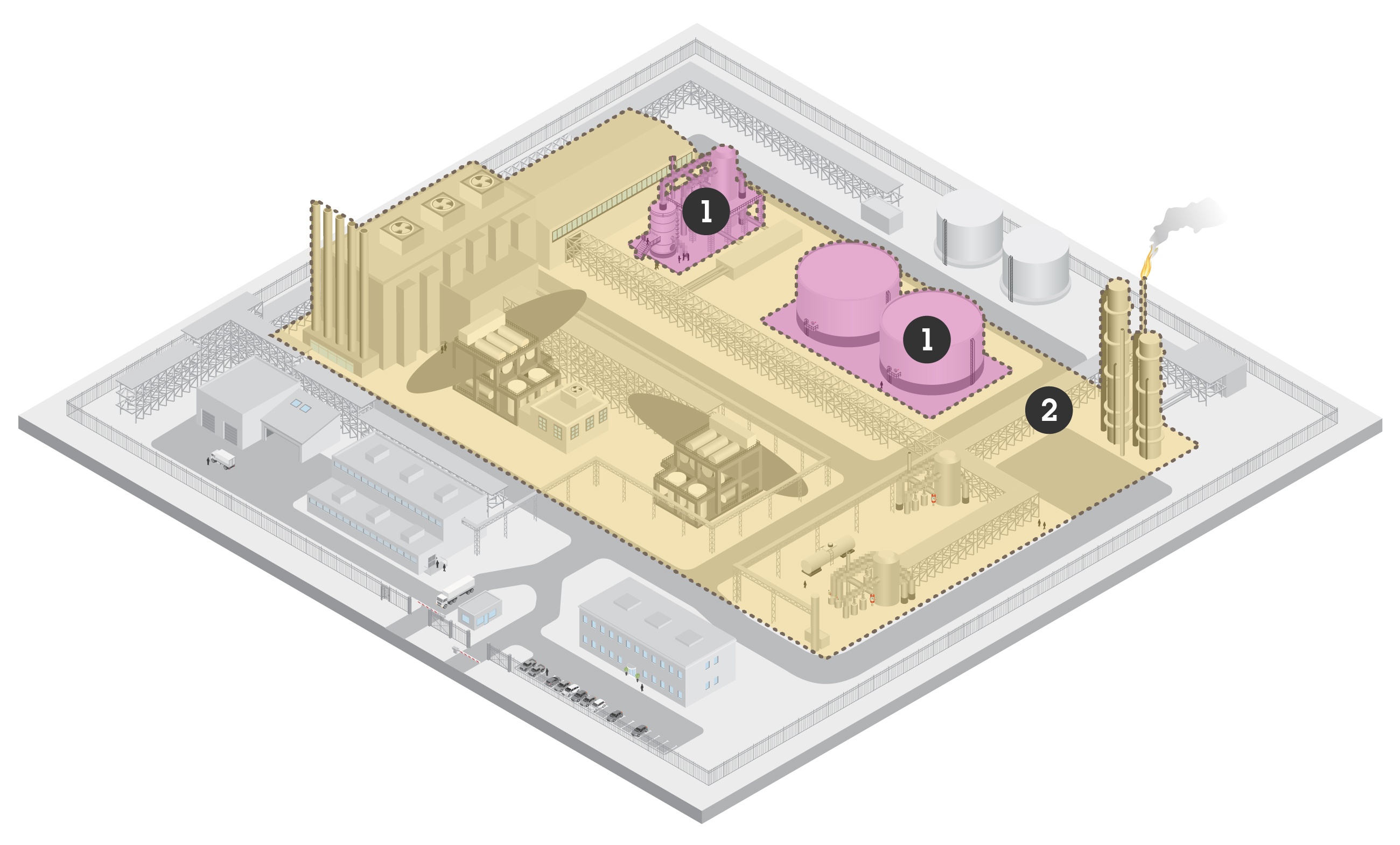
- Zone 0 or Zone 1 areas
- Zone 2 area
Groups of apparatus
For the certification of explosion-protected equipment, all types of apparatus are divided into three groups. Group I covers equipment used in mines and Groups II and III cover all other applications.
Application | Group | Sub-group | Concerns applications where hazards due to the following substance(s) may exist |
---|---|---|---|
Mining | I | Methane | |
Explosive gases | II | A | Propane, methane, and similar gases |
B | Ethylene and other such industrial gases | ||
C | Acetylene, hydrogen, and other very easily ignited gases | ||
Combustible dusts | III | A | Flammable particles |
B | Non-conductive dust | ||
C | Conductive dust |
IIC is the group with the lowest ignition energy (i.e., easiest to ignite) for a gaseous atmosphere. Products certified for IIC can be used also in environments that require equipment to be IIB or IIA classified. Similarly, IIB products can be used in environments that require equipment to be IIA classified. For dust environments, the case is similar and the group with the lowest ignition energy is IIIC.
Product marking
All electrical equipment certified for use in hazardous areas must be labeled to show the type and level of protection applied.
In Europe, the label must show the CE mark and the code number of the notified body that monitors the quality system of the manufacturer. The CE mark is complemented with the ATEX Ex symbol, followed by the group, category and, if Group II equipment, whether the marking relates to gases (G) or dust (D). The marking further specifies the type of protection, the group of apparatus, the temperature category, and the equipment protection level.

- Manufacturer of the equipment
- Certified operating temperature
- Certified camera housing
- ATEX and IECEx certificate numbers, test laboratories, and national certified body
- IECEx marking
- CE mark and notified body auditing the quality system
- ATEX-specific addition to IECEx marking
The tables below provide quick guides to product marking according to the ATEX standard.
Equipment group | Equipment category | Surrounding atmosphere | Explosion protected |
I: Mines II: Surface industry | 1: Zone 0 (or 20) 2: Zone 1 (or 21) 3: Zone 2 (or 22) | G: Gas D: Dust | Ex |
Type of protection | Gas group | Temperature code | Equipment protection level |
d: Flameproof enclosure b: Zone 1 | IIA: Methane IIB: Ethylene IIC: Hydrogen | Gas: T1–T6 T5: 100 °C | G: Gas b: Zone 1 |
Explosive atmosphere | Equipment category | Surrounding atmosphere | Explosion protected |
I: Mines II: Surface industry | 1: Zone 0 (or 20) 2: Zone 1 (or 21) 3: Zone 2 (or 22) | G: Gas D: Dust | Ex |
Type of protection | Dust group | Max. surface temperature | Equipment protection level |
t: By enclosure b: Zone 21 | IIIA: Combustible flyings IIIB: Non-conductive dust IIIC: Conductive dust | 100 °C | D: Dust b: Zone 21 |
The Class/Division system
The authority in charge of the applicable regulation in the US is the Occupational Safety and Health Association (OSHA). In Canada, the authority in charge is CSA.
OSHA points to the National Electric Code (NEC) of the NFPA 70 (published by National Fire Protection Association), or more specifically the NEC articles 500-503 which regulate the classification. OSHA also supplies a list of test standards in accordance with NEC, for electrical products installed in hazardous areas, as well as a list of nationally recognized testing laboratories (NRTL).
Several test standards, such as FM3600, FM3615, and UL1203, can be used for certification according to the Class/Division system.
The testing according to a specific standard must be performed by a test laboratory that is officially recognized as an NRTL for testing against that standard. Examples of laboratories include FM, UL, CSA, MET, and DEKRA. While also issuing the test standards, these laboratories are generally approved for testing according to the other laboratories’ standards, as well as their own.
Classes
The classes are defined according to the type of explosive or ignitable substances that may be present in the atmosphere.
Class | Substances present | |
---|---|---|
I | Flammable vapor or gas | |
II | Combustible dust | |
III | Ignitable fibers or flyings |
Class I locations are those in which flammable vapors and gases may be present. Class II locations are those in which combustible dust may be present. Class III locations are those that are hazardous because of the presence of easily ignitable fibers or flyings.
Divisions
Each of the three classes is further subdivided into Division 1 or Division 2. The division is defined according to the likelihood of the hazardous material being present in a flammable concentration. Equipment approved for Division 1 can also be used in Division 2 within the same class.
Division | Definition | |
---|---|---|
1 | In which ignitable concentrations of hazards exist under normal operation conditions and/or where hazard is caused by frequent maintenance or repair work or frequent equipment failure. | |
2 | In which ignitable concentrations of hazards are handled, processed, or used, but which are normally in closed containers or closed systems from which they can escape only through accidental rupture or breakdown of such containers or systems. |
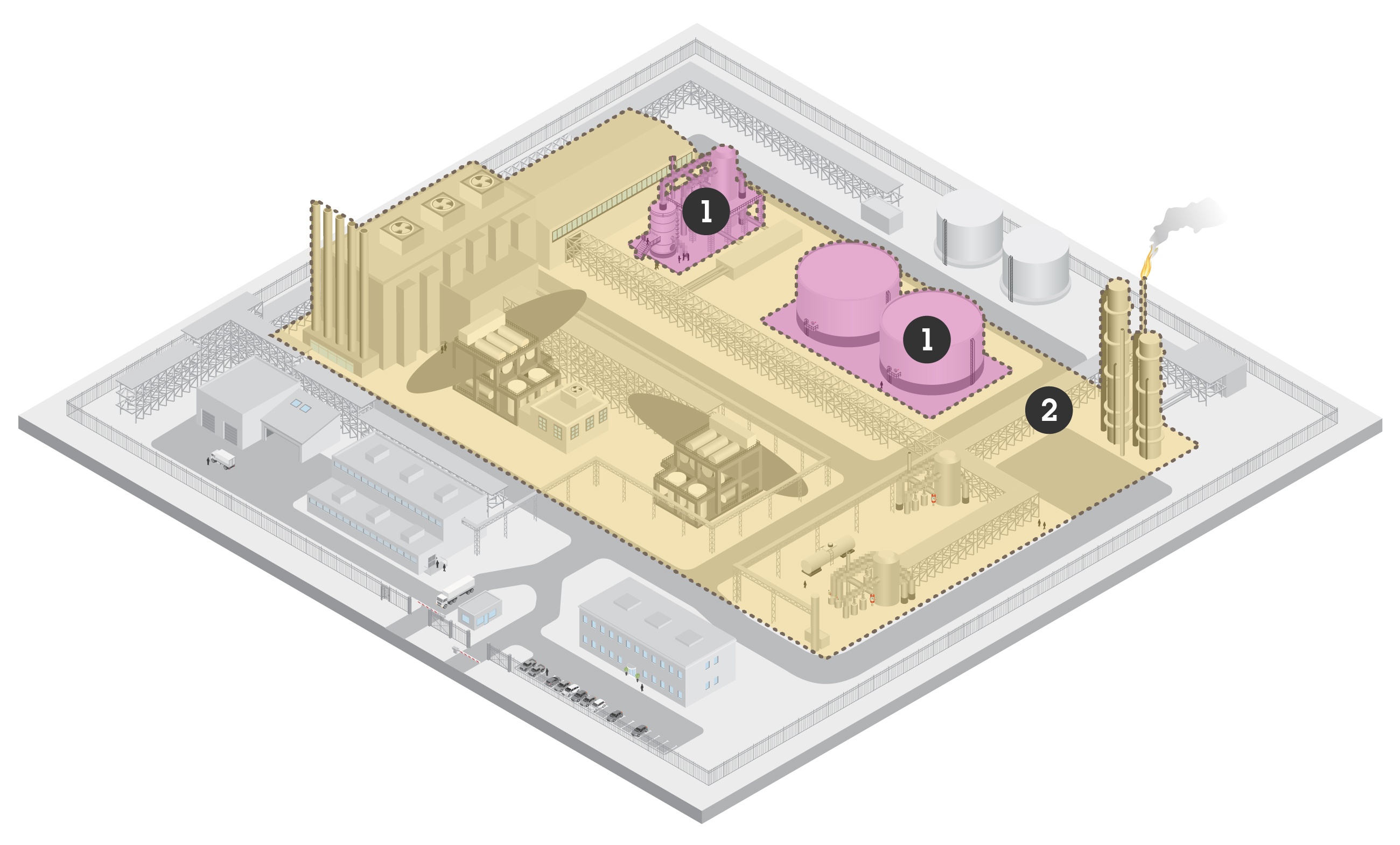
- Division 1 areas
- Division 2 area
In a Division 2 area, an explosive atmosphere is present only under abnormal conditions.
In a Division 1 area, explosive atmospheres will occur continuously or intermittent periodically more than ten hours per year. This is typically inside tanks filled with flammable liquids, and in the proximity of valves.
Groups
The three classes are also subdivided into groups of hazardous materials. The groups are associated with substances rated by how flammable they are, which is based on, among other things, maximum explosion pressures. The tables below show typical flammable material of each group. The materials represent certain ignition energies, for which the equipment is safe.
Group | Flammable material (examples) of Class I (vapor or gas) | |
---|---|---|
A | Acetylene | |
B | Hydrogen | |
C | Ethylene | |
D | Propane |
Group | Flammable material (examples) of Class II and III (combustible dust and ignitable fibers or flyings) |
---|---|
E | Metal dusts |
F | Carbonaceous dusts |
G | Combustible dusts |
Product marking
All electrical equipment certified for use in hazardous areas must be labeled to show the type and level of protection applied.
In North America, explosion-protected products must be equipped with a marking label that specifies the manufacturer, the certificate issuer and file number, and the marking according to NFPA 70 (NEC article 500-506) and CSA C22.1.
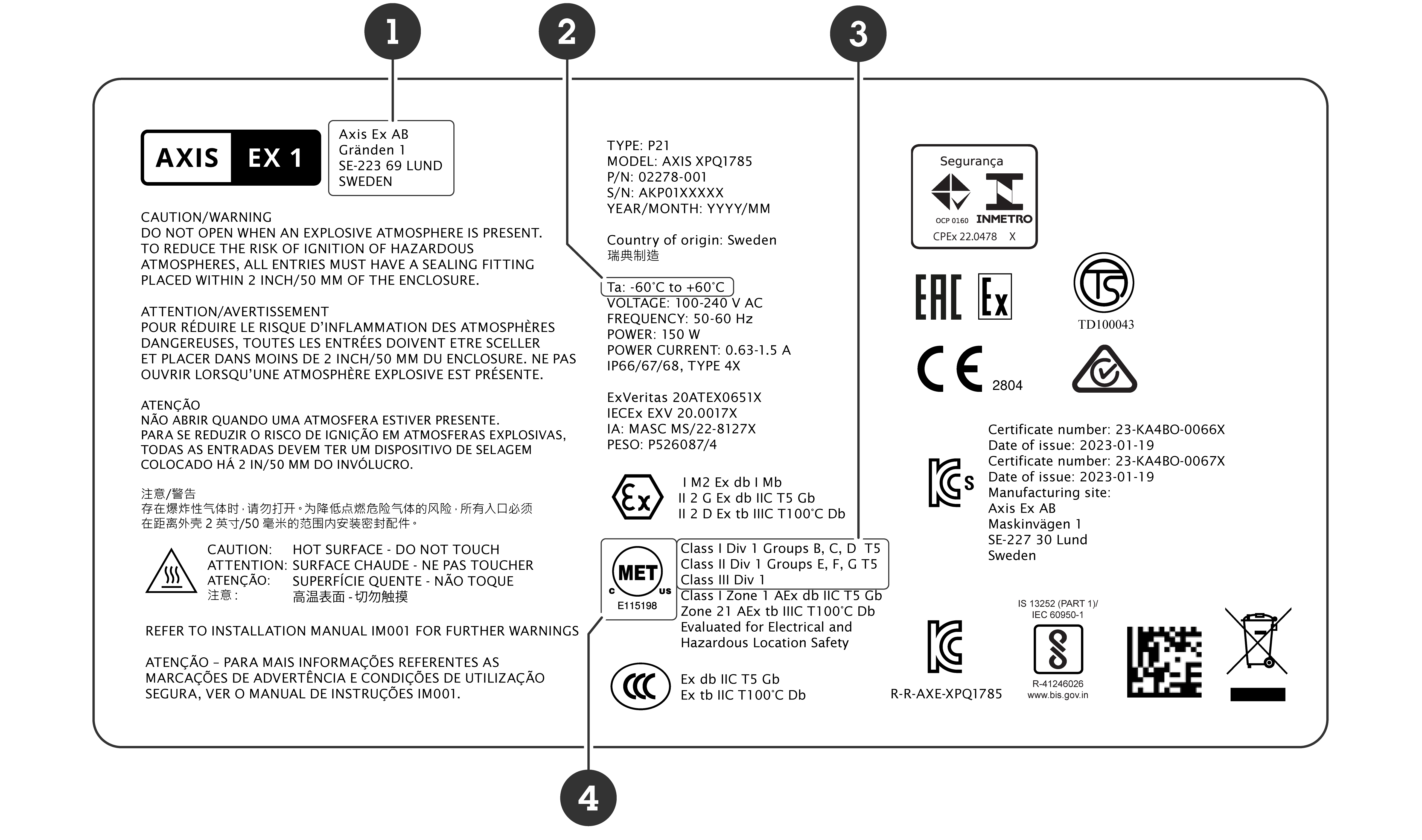
- Manufacturer of the equipment
- Certified operating temperature
- Marking according to NFPA 70 article 500-503 and CSA C22.1 appendix J
- National Recognized Test Laboratory (NRTL) and issuer of the certificate and certificate (file) number
The table provides a quick guide to product marking according to the Class/Division system.
Explosive atmosphere | Area classification | Gas/dust group | Temperature code |
---|---|---|---|
Class I: Gas/Vapor Class II: Dust Class III: Flyings | Division 1 Division 2 | A: Acetylene B: Hydrogen C: Ethylene D: Propane E: Metal dusts F: Carbonaceous dusts G: Combustible dusts | T1–T6 T5: 100 °C (Maximum surface temperature of equipment) |
The Class/Zone system
The Class/Zone system used in North America combines the traditional Class/Division system used in North America with the international IEC Zone system.
The authority in charge of the applicable regulation in the US is the Occupational Safety and Health Association (OSHA). In Canada, the authority in charge is CSA.
OSHA points to the National Electric Code (NEC) of the NFPA 70 (published by National Fire Protection Association), or more specifically the NEC articles 505-506 which regulate the classification. OSHA also supplies a list of test standards in accordance with NEC, for electrical products installed in hazardous areas, as well as a list of nationally recognized testing laboratories (NRTL).
The ISA/UL 60079 series of standards can be used for certification according to the Class/Zone system.
The testing according to a specific standard must be performed by a test laboratory that is officially recognized as an NRTL for testing against that standard. Examples of laboratories include FM, UL, CSA, MET, and DEKRA. While also issuing the test standards, these laboratories are generally approved for testing according to the other laboratories’ standards, as well as their own.
Classes
In the Class/Zone system, the designation of Class I for gas is the same as in the Class/Division system. Class II and III designations, however, are not used but are instead implied by Zones 20, 21, 22 and dust groups IIIA, IIIB, IIIC.
Class | Substances present | |
---|---|---|
I | Flammable vapor or gas |
Zones
Hazardous areas are divided into zones. The zone is defined by the probability that hazardous material will be present in an ignitable concentration in the surrounding atmosphere.
Zone | Hours per year of flammable gas-air mixture or dust clouds present | |
---|---|---|
Gas | Dust | |
0 | 20 | 1000 or more hours/year (10%) |
1 | 21 | 10 < hours/year < 1000 (0.1% - 10%) |
2 | 22 | 1 < hours/year < 10 (0.01% - 0.1%) |
For gases, Zone 0 is an area in which an explosive gas-air mixture is continuously or frequently present, or present for lengthy periods. Zone 1 is an area in which an explosive gas-air mixture is likely to occur for short periods during normal operation. In Zone 2, an explosive gas-air mixture is not likely to occur. If it does occur, it will exist due to abnormal conditions and for a very short time.
For clouds of combustible or conductive dusts, the equivalent zones are 20, 21, and 22.
Zones 1 and 2 (or 21 and 22 for dust) are the most common classifications, whereas Zone 0 (or 20 for dust) is restricted to small, inaccessible areas or areas inside technical equipment. Products certified for Zone 0 (20) can be used in Zones 0, 1, and 2 (20, 21, and 22). Zone 1-certified (21) products can be used in Zones 1 and 2 (21 and 22).
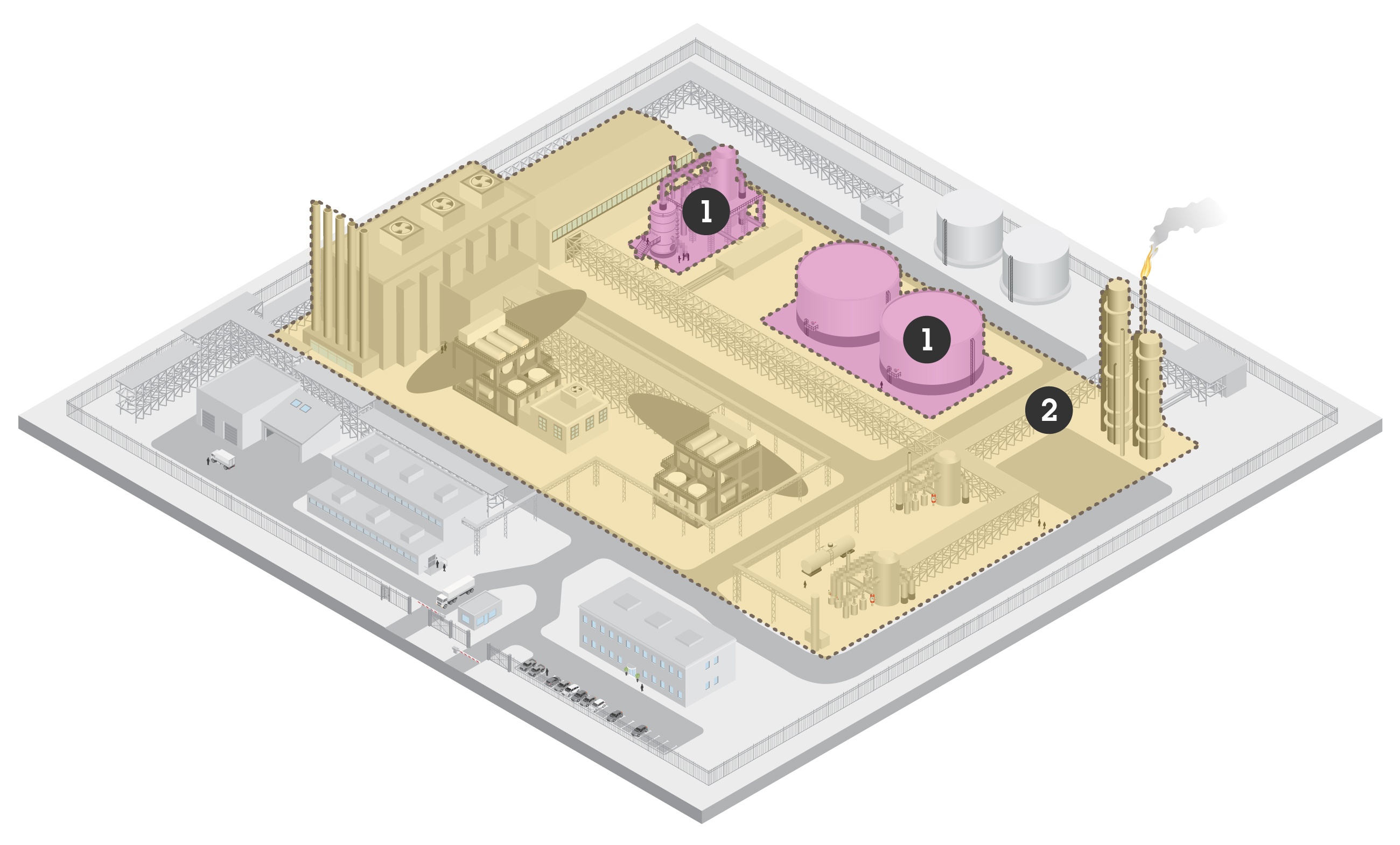
- Zone 0 or Zone 1 areas
- Zone 2 area
Groups of apparatus
For the certification of explosion-protected equipment, all types of apparatus are divided into three groups. Group I covers equipment used in mines and Groups II and III cover all other applications.
Application | Group | Sub-group | Concerns applications where hazards due to the following substance(s) may exist |
---|---|---|---|
Mining | I | Methane | |
Explosive gases | II | A | Propane, methane, and similar gases |
B | Ethylene and other such industrial gases | ||
C | Acetylene, hydrogen, and other very easily ignited gases | ||
Combustible dusts | III | A | Flammable particles |
B | Non-conductive dust | ||
C | Conductive dust |
IIC is the group with the lowest ignition energy (i.e., easiest to ignite) for a gaseous atmosphere. Products certified for IIC can be used also in environments that require equipment to be IIB or IIA classified. Similarly, IIB products can be used in environments that require equipment to be IIA classified. For dust environments, the case is similar and the group with the lowest ignition energy is IIIC.
Product marking
All electrical equipment certified for use in hazardous areas must be labeled to show the type and level of protection applied.
In North America, explosion-protected products must be equipped with a marking label that specifies the manufacturer, the certificate issuer and file number, and the marking according to NFPA 70 (NEC article 500-506) and CSA C22.1.
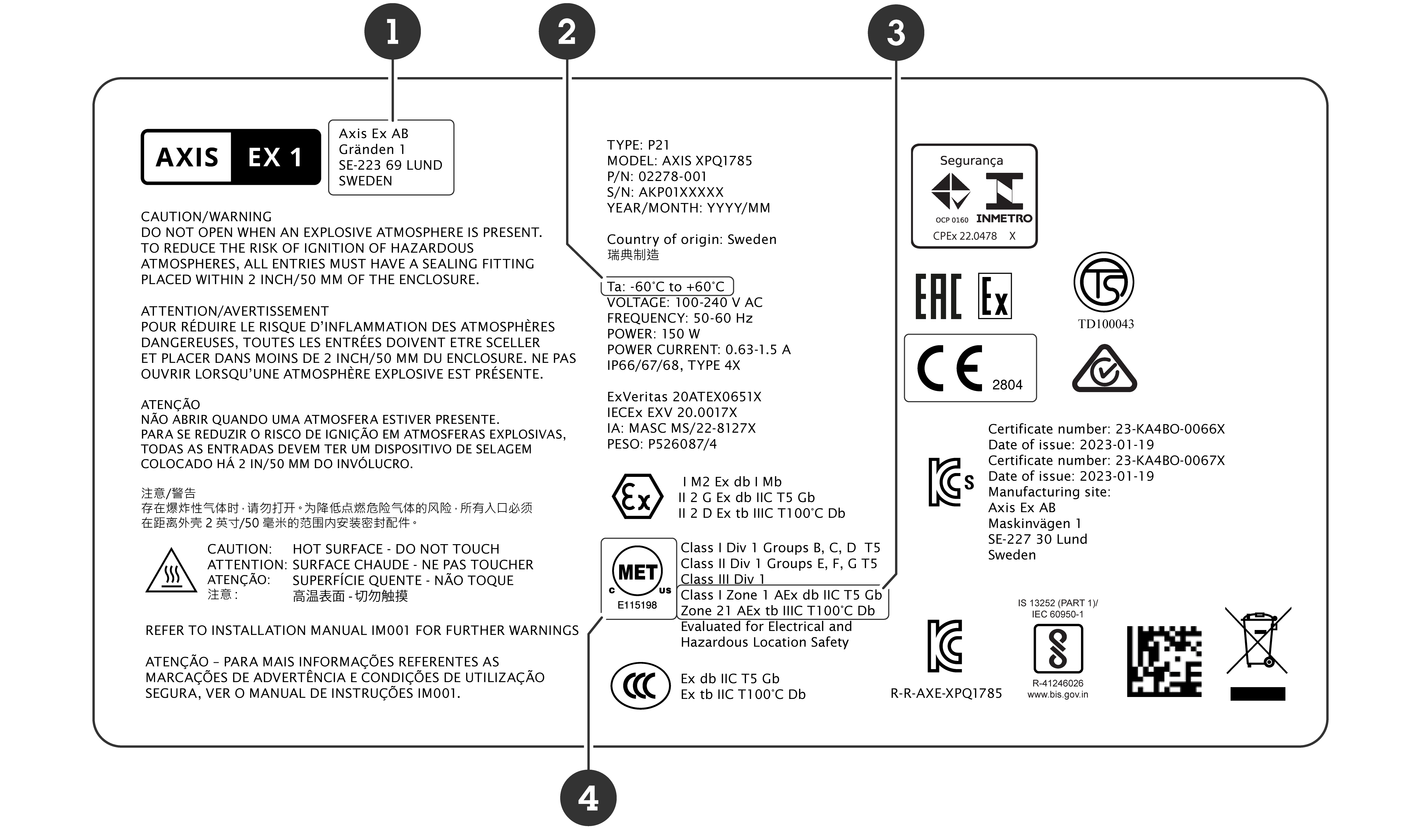
- Manufacturer of the equipment
- Certified operating temperature
- Marking according to NFPA 70 article 505–506 and CSA C22.1 article 1818
- National Recognized Test Laboratory (NRTL) and issuer of the certificate and certificate (file) number
The table provides a quick guide to product marking according to the Class/Zone system.
Explosive atmosphere | Area classification | Gas/dust group | Temperature code |
---|---|---|---|
Class I: Gas/Vapor (For dust environments, the class of the hazard (Class II) shall not be mentioned in the marking.) | Zone 0 (Gas) Zone 1 (Gas) Zone 2 (Gas) Zone 20 (Dust) Zone 21 (Dust) Zone 22 (Dust) | IIA: Propane IIB: Ethylene IIC: Acetylene IIIA: Combustible flyings IIIB: Non-conductive dusts IIIC: Conductive dusts | Gas: T1–T6 T5: 100 °C (Maximum surface temperature of equipment) |
Comparisons between the systems
This section displays tables for easy comparison between the systems.
Zone 0 | Zone 1 | Zone 2 |
Where ignitable concentrations of flammable gases, vapors, or liquids are present continuously or for long periods of time under normal operating conditions. | Where ignitable concentrations of flammable gases, vapors, or liquids: | Where ignitable concentrations of flammable gases, vapors, or liquids: |
Division 1 | Division 2 | |
Where ignitable concentrations of flammable gases, vapors, or liquids: | Where ignitable concentrations of flammable gases, vapors, or liquids: |
Groups used with IEC Zone system and Class/Zone system | Groups used with Class/Division system |
---|---|
IIC — Acetylene and hydrogen | A — Acetylene |
B — Hydrogen | |
IIB — Ethylene | C — Ethylene |
IIA — Propane | D — Propane |
Axis explosion-protected devices
To select the proper equipment for hazardous areas you first perform an area classification to define the probability of hazardous materials being present. This means identifying which type of explosive or ignitable substance that the equipment might be exposed to, the concentration, and the duration of the exposure. If the result is that ignitable concentrations are likely to exist for short periods during normal operation, the area is a Zone/Division 1 area. If ignitable concentrations are not likely to exist, except in case of abnormal conditions and only for very short periods of time, the area is a Zone/Division 2 area.
Axis devices certified for Zone/Division 1 areas are protected through the protection methods Ex d (enclosure prevents any potential flame propagation from an internal explosion spreading to the surrounding gas mixture — “flameproof” (ATEX/IECEx) or “explosionproof” (US/CAN)) and Ex t (enclosure restricts the surface temperature and keeps ignitable dust out from the electronics — “dust ignition protection” (ATEX/IECEx) or “dust-ignitionproof” (US/CAN)). These are heavy-duty, robust enclosures usually made from stainless steel or aluminum. This gives a fairly heavy product.
Axis devices certified for Zone/Division 2 areas are protected through the protection method Ex e: increased safety (ATEX/IECEx) or nonincendive electrical equipment (US/CAN). The protection here lies in the mechanics and electronic components. By design, the device can’t provide sufficient energy to ignite the gas or dust (there will be no arcs, sparks, or hot surfaces), and no extra enclosure is needed around the device. This results in a significantly lighter and more compact device.
Proper design of hazardous areas aims at limiting the potentially combustible areas as much as possible. Hence, Zone/Division 2 areas are significantly more common than Zone/Division 1 areas. Zone/Division 2 areas are less hazardous than Zone/Division 1 areas in that explosive atmospheres are not likely to occur in Zone/Division 2 during normal operating conditions. However, when you have an explosive atmosphere in Zone/Division 2, it’s equally hazardous as Zone/Division 1.
Devices certified for Zone/Division 1 areas can also be used in Zone/Division 2 areas, but Axis devices specifically designed and certified for Zone/Division 2 areas are a more cost-efficient alternative. Both installation costs and purchasing costs are kept down, while the devices are sturdy with outdoor rating for impact, cold weather, and rain.
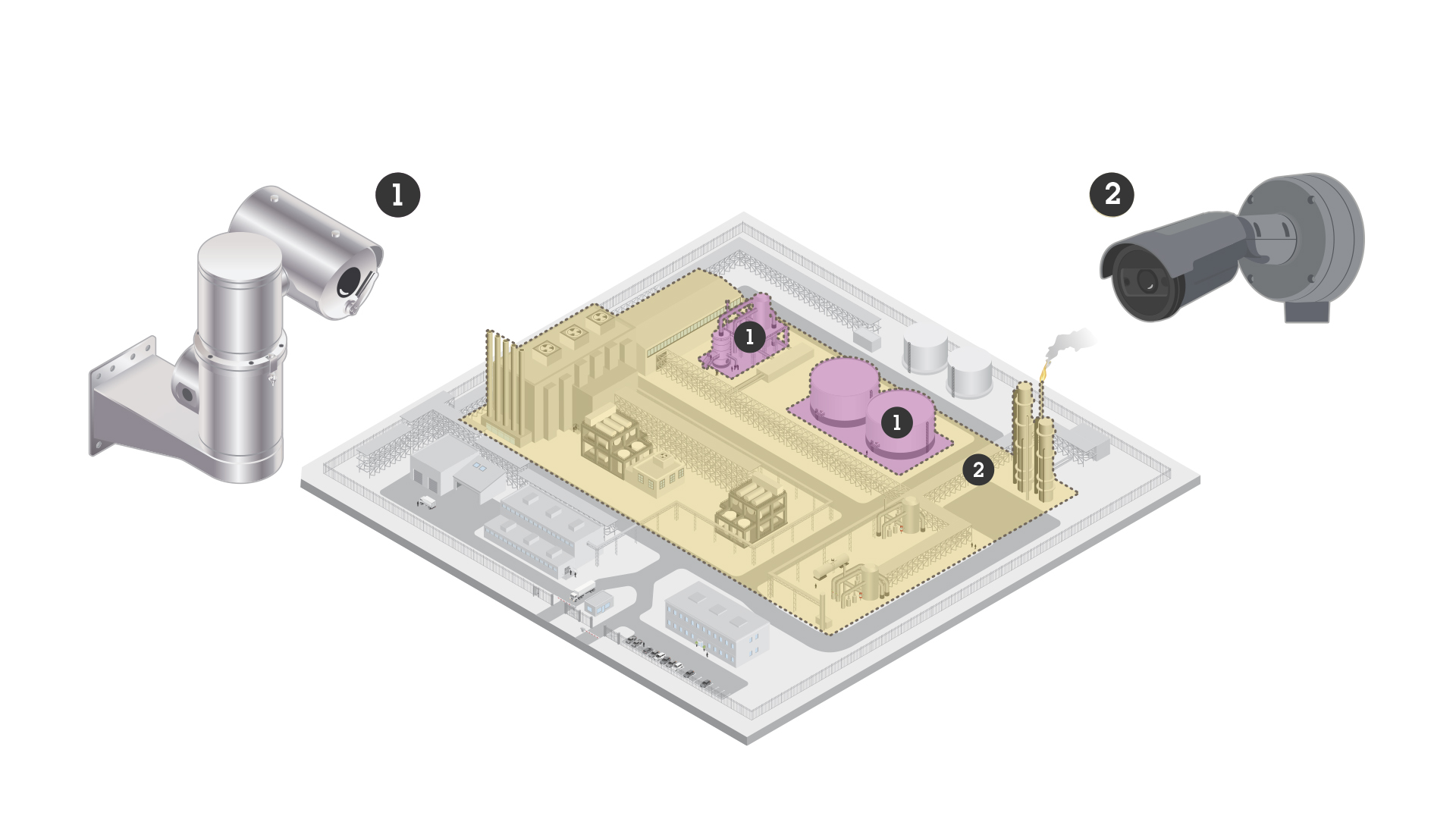
- In Zone/Division 1 areas you must use a device specifically certified for Zone/Division 1 areas.
- In the more common Zone/Division 2 areas you can also use the lighter and more cost-efficient device certified for Zone/Division 2 areas.