Tested without compromise
Summary
Ensuring hardware quality in Axis products starts from the design phase, where components are carefully selected, partly for their own qualities, and partly for how well they function in combination with the other included components. The concept design is reviewed and potential risks are highlighted and addressed.
Axis products are subjected to many different tests during development: impact tests to assess their robustness, ingress tests to determine how well they keep objects and water out, vibration tests to evaluate the risk of damage or impaired function, and climate tests to ensure protection against extremes of temperature. For Axis, it is important that the products not only pass the standards for approval, but also work great in reality.
All Axis products are also tested thoroughly during production, using both automatic and manual tests. For superior resistance to impact, Axis uses polycarbonate (PC) and glass for products’ windows and polycarbonate (PC) for domes.
Introduction
Axis products are designed for reliability such that they can withstand harsh environments and usage. During development, Axis products spend over a year in test environments, where they are tested for their ability to withstand mechanical wear and tear, water and humidity, vandalism, extreme temperatures, vibration, and more. Products are certified to external standards, but Axis testing also goes beyond the required quality approvals.
Axis has in-house test labs with top class equipment. They are used for performing several tests and gaining more knowledge, all of which contributes to the development of better products. Also with these labs, Axis hardware designers can participate and see the test performance firsthand and gain better insights into improving the product.
This document summarizes how the hardware quality of Axis products is ensured through thorough and exhaustive testing.
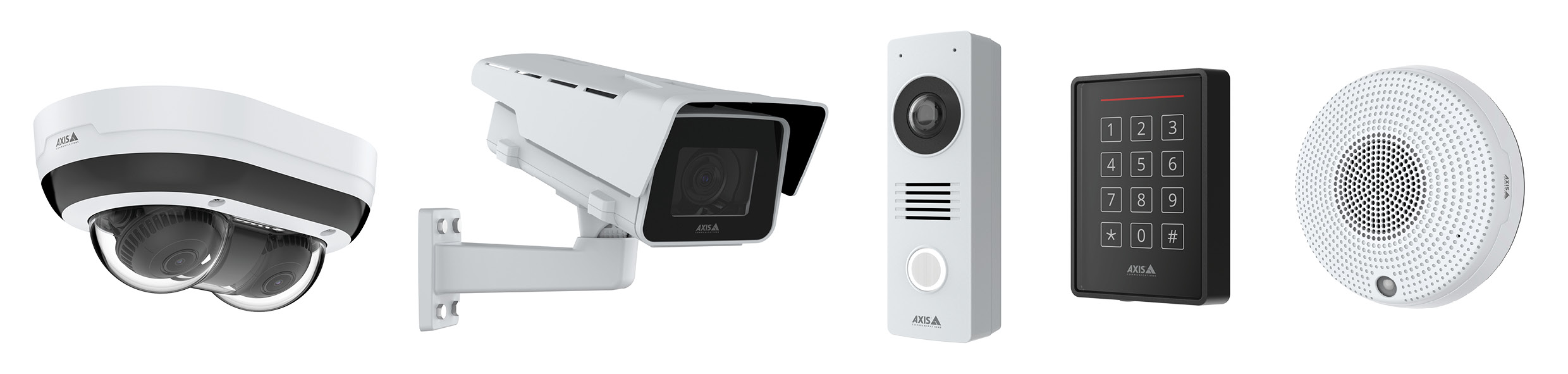
High-quality design and components
The quality work at Axis starts during the concept design phase. Field data and experience of the predecessor are first used to design an improved new product. Axis sets components’ requirements for suppliers, such as lens requirements, to ensure high component quality. The environmental footprint of the materials are also considered in minimizing environmental impact.
Axis pays high attention to the thermal design to ensure better cooling for the image sensor, resulting in less visible noise and better image quality. Furthermore, circuit boards are always enclosed in a casing for protection against physical or weather damage, and against electrostatic discharge. Cables and connectors in the products are shielded to withstand electrical surges and induction from surrounding power cables.
The design evolves through several iterations until the final design meets all requirements. In the early stage of the design and with the use of Finite Element Analysis (FEA) computer programs, Axis simulates climate conditions (warm or cold) and external mechanical impacts (IK test) to assess the safety of the product’s inner equipment for potential issues and update the design before building prototypes. This increases the quality of the product even before testing begins.
It is not only the individual details that affect quality; the combination of details in the product as a whole is equally important. Consider the camera lens as an example; many vendors sell security cameras without a lens, leaving it to the customer to try to find the most suitable one. Today’s market offers an abundance of lenses and cameras with a wide variety of resolutions and image enhancement technologies, making it quite a challenge to match the right camera with the right lens. Axis cameras, on the other hand, are always sold with a lens, one that is optimized for the sensor and chassis of the camera, using Axis’ proprietary system of active alignment.
Durability tests
Products should pass durability tests to show that the products have long lifespan and are reliable and accurate over time. Several durability tests are done to ensure product quality before placing them in the market.
An example is the PTZ camera durability test that checks the camera’s performance with roughly 10 000 000 movements of the pan, tilt, and zoom. After the test, the camera must remain very accurate when moving to preset positions without any degradation of the user experience.
For reliability, the products and its moving parts must maintain excellent quality for many years without degradation. Some of the other durability tests include cycling of pan, tilt, zoom, focus, day/night-filter, wiper, cables, buttons, and memory cards.
Impact resistance tests
Many devices such as security cameras are placed in environments where they might be subjected to various impacts. The most obvious example is vandalism and other physical attacks on the device, but it can also be branches and debris striking the device on a windy day, birds and other animals sitting or climbing on the device, or an occasional drop of the device during installation.
Impact resistance tests are performed according to European standard (EN) and International Electrotechnical Commission (IEC) standard EN/IEC 62262. The IK rating of the standard specifies to what extent an enclosure protects its contents from external impact. The tests are used to demonstrate an acceptable level of robustness when assessing the safety of a product, and are primarily intended for testing the enclosure of electrotechnical items.
The development of a robust enclosure starts early, before building the physical mechanical parts. Axis simulation engineers simulate the test in FEA model to check for weak points and potential risks. The design is then updated based on the results of the simulation.
According to EN/IEC 62262, IK tests should be performed as follows: each exposed surface of the product should be hit five times, evenly distributed over the surface. This means that the products are hit up to 30 times on different positions and on different sides. A standard IEC probe, with a mass of 0.25–10 kg (0.55–22 lb), is selected for use according to the IK rating. Axis products are tested using both the vertical and the pendulum hammer methods.
According to Axis’ criteria, the impact points are selected from the weakest points of the product. This selection is an important distinction, since the standard itself does not define that the product needs to be tested at its weakest points. It is quite possible for a manufacturer to choose the strongest points of the product when testing for IK rating, leading to a successful test result, but possibly to a less robust product.
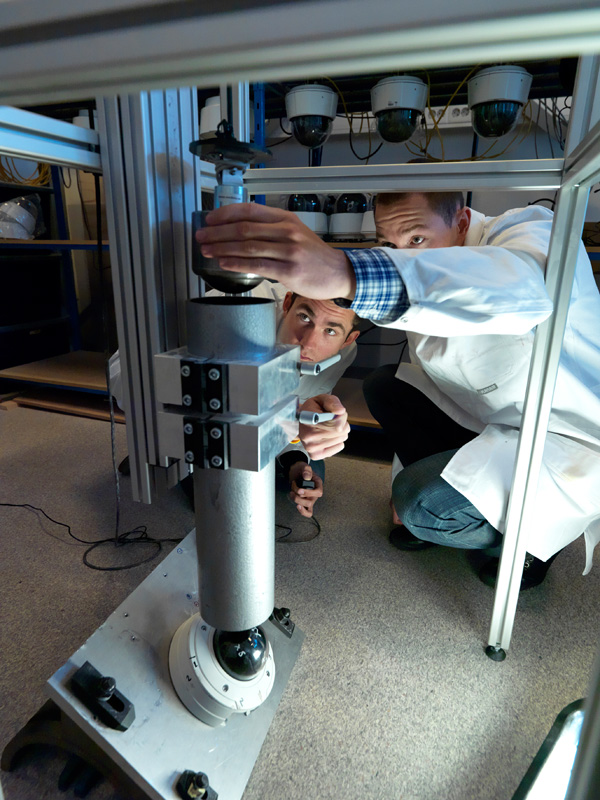
After the test, the product should still meet the stated IP rating, meaning that the product retains its water and dust resistance even after being severely impacted from many angles (see the section Ingress protection tests for more information on IP tests). There should be no permanent deviation inside the enclosure that affect the function of the product, nor should any internal electrical components have failed or deteriorated.
Axis products are designed based on lessons learned from previous tests, coupled with the latest technology. A high-speed camera is often used during prototype testing to analyze dome deformation and mechanical behavior during the impact. This gives the mechanical engineers relevant information needed to update the design and improve impact resistance.
Corrosion tests
Corrosive environments and elements can impact the operability and physical look of a product. Corrosion tests such as NEMA 4X salt spray and ISO 21207, and product exposure to corrosion attacks are conducted to test and improve product durability, quality, and reliability.
These tests shows if a product can withstand exposure to corrosive gases, salt, and high humidity without suffering any critical damage to its casing and internal components. A high humidity test is also included because products in very humid environments can have moisture buildup. Corrosion can occur when a product can’t withstand such humidity level.
NEMA 4X salt spray: NEMA 4Xcertification involves several tests and one of them is NEMA 4X salt spray. It is important that all outdoor products are designed to withstand exposure to salt. To do this test, products are sprayed with saltwater for up to 600 hours to check their housings’ resistance level.
ISO 21207, salt spray, and corrosive gases: ISO 21207, also known as ‘corrosion tests in artificial atmospheres’ is an accelerated corrosion test that exposes products to corrosive gases and salt spray. This test assesses the corrosion resistance of products to corrosive environments. It is very essential for products that are used in traffic and industrial environments. ISO 21207 consists of two methods; first method uses exposure to salt spray, corrosive gases, controlled drying and humidity while the second method uses same exposure except for corrosive gases.
After these tests, the test engineers check for corrosion attacks and defects on the products. Corrosion attacks such as rust on internal components are not acceptable after testing.
Ingress protection tests (IP tests)
The installation environment can have a powerful effect on product operability. Water can penetrate products that are exposed to rain and impair their functionality. In severe cases, products exposed to water can fail and expose the public to potential electrical hazards. Products mounted at construction sites, mining operations, transportation systems and similar environments, are subjected to high levels of dust and other air particles. For example, dust can impair image quality or render a camera inoperable. Axis products are tested for both dust and water resistance.
For the ingress protection of a product, Axis uses the IEC/EN 60529 standard that specifies IP-classification (IPXY) where ‘X’ is a number between 0 and 6, and ‘Y’ is a number between 0 and 9. The first digit indicates the degree of protection against the intrusion of solid objects, such as dust, and the second indicates protection against water. IP tests should be performed both before and after the impact test.
For IP66, the IP class for most Axis outdoor products, the procedure consists of two tests. In the first test, the product is placed in a dust chamber and subjected to extremely high levels of fine grain talc, at a negative pressure of 20 mbar (15 mmHg, 0.29 psi), for a period of 2 hours. The dust level is high enough to present severe health risk to anyone exposed to it for a prolonged period of time. After hours of dust exposure, the product is carefully opened and checked for any dust because no dust should pass through the product’s housing to get inside the product. This test is a good indicator of the housing integrity of a product and the quality of its sealing gaskets.
In the second test, the product is exposed to a high-pressure water jet, with a flow rate of 100 l/ minute (26 gallons/minute) from a distance of 2.5-3 m (8ft 2 in-9ft 10in) on all exposed surfaces from different angles. Water shouldn’t penetrate the product. Following the test, the product is opened and inspected for water ingress, with special attention paid to its sealing gaskets. The product functionality is also thoroughly checked.

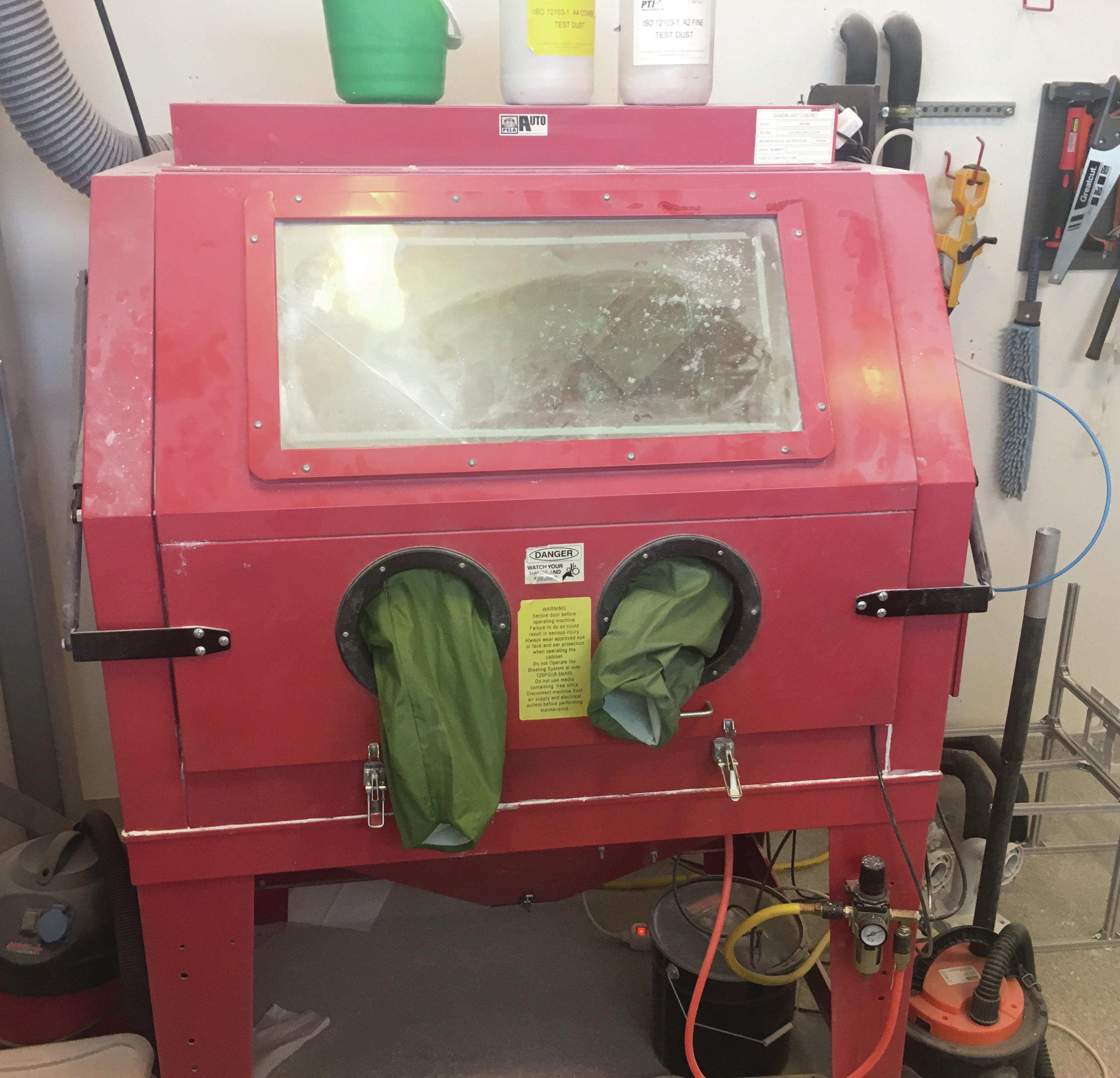
Vibration tests
A product can be subjected to vibrations from many sources in its installation environment. It could be located by a server room, in a factory, near traffic, or mounted on a vehicle and can also be exposed to regular vibrations when shipped to a customer. Over time, vibration can cause changes in product functionality, such as a camera’s loss of focus or other mechanical properties. The ability to maintain focus during low-level vibrations is critical for the image quality of any camera. Excessive vibration can also wear down screws and other components, leading to permanent damage and product failure.
Axis products undergo three types of vibration tests: vibration robustness tests, vibration performance tests, and shipment tests. Robustness tests check how a product works after being subjected to high level of vibrations and shocks, and performance tests check image stability during vibrations. Shipment tests evaluate whether a product will function properly after being transported in its packaging to the end user.
Robustness test
Axis robustness tests are highly accelerated tests that verify if a product can handle vibrations and shocks during its lifetime. These tests determine that the product and its materials are robust enough to survive vibrations and shocks. The test levels depend on each product’s use case and environment. For example, onboard products (products used on trains, buses and in cars) are tested at higher levels than products made for indoor ceiling mount. Also, products like door stations are subjected to shocks that are up to 50G because such products can be mounted close to slamming doors.
Most products are tested for vibration according to IEC 60068-2-6 and tested for shock according to IEC 60068- 2-27. Following the tests, the product is closely examined for loose screws, mechanical defects, material failure and other key mechanical properties.
The product must pass the test to ensure that it still operates well after each test. After the product has been subjected to the robustness test, there should be no permanent defocusing or functional problems. The product should always be able to refocus and work properly.
Performance tests
While the robustness tests are highly accelerated, the performance tests are at expected real-life levels, with high attention to user experience during the test. Axis engineers have measured vibration and shock levels at various locations and simulate these scenarios in the laboratory, to ensure good image quality during vibration. The purpose of the test is to measure qualities that are not defined in standards but are of special interest to a project.
For example, these tests check the positioning of products, so they don’t lose their preset positions and also check the focus and image stability of cameras when exposed to real-life vibration and shock scenarios.
Shipment tests
Shipment tests are performed to ensure that a product arrives fully functional at the customer’s site. As the size of the product increases, these tests become more important. Units failing at arrival delays customer projects and can be costly, so it is very important that the product is in good condition even after a rough handling.
Shipment tests are run on packages to determine the integrity of the packaging and its ability to protect the product. According to the International Safe Transit Association (ISTA) standard for parcel delivery shipment, the shipment tests consist of vibration and drop test. For example, a product, packed in the intended packaging, is placed on a platform. It is then subjected to a random vibration profile that accelerate conditions inside a delivery truck driving on a bad road. A typical test simulates thousands of miles travelled by road and air. For the drop test, Axis conducts 17 drops of the product’s face, edges, and corners on a concrete surface while in its packaging. The drop test is done from a free fall height of 46 to 91 cm. Axis packaging engineers design good packages that are strong enough to protect the product from damage.

Abrasion tests
Abrasion tests, according to the ISO 11998 standard, are performed in a lab to check whether the surfaces protecting the lens, such as polycarbonate windows or domes, are resistant to abrasive materials. The products are scrubbed with an abrasive cleaning pad and soap water, with a predetermined pressure against the tested products’ surface. Each product is subjected to 100 cycles. After the test, the product should still function properly, with maintained image quality. It should also be aesthetically pleasing.
Chemical resistance test
Products’ resistance to cleaning agents is becoming more important to customers, especially for products that are installed in highly hygienic environments like laboratories and hospitals. In such environments, a product’s exterior could be cleaned several times daily. Cleaning of products is also important in other environments like prisons, mines, industrial environments, highway stations, and ports.
Chemical resistance tests are complex because it depends on the nature of chemical contact, such as composition of the chemical, exposure time, temperature, and the level and type of stress the product is subjected to. For this reason, the product materials are tested in real user scenarios.
The chemical resistance is tested through two types of in-house testing: “Environmental Stress Crack Test” and “ Cleaning Test”. The chemicals that are used for these tests are Isopropanol (70%), Hydrogen peroxide (3%), and Sodium hypochlorite (< 5%). These chemical solutions are commonly used as cleansers or disinfectants for healthcare equipment.
Environmental Stress Crack Test (ESC): ESC test is based on ISO 22088-3, "Plastics - Determination of resistance to environmental stress cracking (ESC) - Part 3: Bent strip method." It evaluates materials resistance to chemicals and help to decide which materials should be used in the products. In an ESC test, a test sample of the material is subjected to mechanical stress in combination with exposure to chemical. During the test, the sample is periodically controlled for cracks, color changes, and other defects. After testing, the sample is again evaluated for defects.
Chemical cleaning test: The cleaning test simulates repeated cleaning with chemical over many years of usage. Samples of the products are mounted in an automated test equipment that repeatedly swipes the samples with a soft cloth saturated with chemical. The swipes are done using a level of pressure that is typical of cleaning, and the cloth is re-saturated regularly. The samples are tested up to 27,500 cycles depending on the intended product environment and usage requirement.
To read more about the recommended cleaning of products, see the white paper Chemical resistance to common cleaning agents on axis.com/learning/white-papers.
Highly Accelerated Life Testing (HALT)
Axis performs Highly Accelerated Life Testing (HALT) to test the reliability of a product by exposing it to extreme conditions, such as temperature extremes, rapid changes in temperature, electrical stress conditions, random vibration, power cycling, and humidity testing. These test conditions simulate the stress conditions a product might encounter in its lifespan, but of higher degree than what is expected from actual use. This helps identify design problems and potential weaknesses in the electrical and mechanical parts.
With the result of HALT, Axis mechanical and electrical engineers further improve the products’ design, quality, reliability, and lifespan.
Climate tests
Axis products are used all over the world, in indoor as well as outdoor environments. They are exposed to enormous variations in temperature – from the searing heat of the Middle East to the icy cold of Alaska. Additionally, some products are mounted on top of poles or buildings, exposing them to extreme wind and sunlight. Consequently, temperature resistance is a critical aspect of any security device.
High or low temperatures can cause components to fail or freeze. Prolonged exposure to even moderately high temperatures reduces the lifespan of equipment. Humidity can cause component damage, but can also cause condensation on the inside of a camera dome leading to bad image quality.
Ensuring that Axis products work reliably in extreme climate conditions is a critical issue during design and production. The datasheet specifies a maximum and minimum operating temperature, as well as a startup temperature. To make sure that all products fulfill the defined values, extensive climate testing is performed, both in labs and at live test sites. Axis products are subjected to extreme temperature and climate conditions in long-term tests in Sweden and in the United Arab Emirates.
Lab tests
Climate tests in labs are performed in climate chambers, where various types of temperatures and climates can be simulated. Tests are made with an interval margin of ±15 °C (±27 °F) at either end of the operational temperature range. The humidity range spans 0 to 100%.

Components as well as complete products are tested. No critical component is allowed to be out of specification when the complete product is tested within its temperature range. This ensures great performance of the product in both low and high temperatures and a long lifespan of the product. Image quality tests are made in different temperatures to ensure image quality across the entire operating temperature range. In addition, condensation performance tests help to check that fog does not build up in front of the lens in different scenarios. All through the test, all functions (e.g. heaters, pan, tilt and zoom, and infrared), system logs and power consumption are checked to ensure the products are running as intended.
Low temperature test
Axis products are guaranteed to start and be fully functional at the temperature range stated in the datasheets, and the cold condition temperature is the most critical. High attention is given to moving parts, such as pan, tilt, zoom and focus so they operate as intended even in extremely cold conditions. De-icing tests confirm how well outdoor products can melt ice and snow that builds up in front of the lens.
High temperature test
Axis products are designed with focus on heat dissipation to decrease the temperature of the image sensor and optics. This keeps the visible noise down even in low light conditions, thanks to their good thermal design. For outdoor products, placing them in sunny environments increases the product’s temperature and this is considered during the product’s development and testing.
Live sites
In addition to extensive lab tests, Axis products also undergo live site testing, to observe long-term effects in real environments, with the aim to develop the best products for real user scenarios. The results give reliable data about condensation, corrosion, mechanical and cosmetic defects, and image quality of the tested products. Climate data, from a weather station mounted next to the products is saved, and analyses are conducted on all environmental parameters that the products are subjected to. The products are monitored around-the-clock for years and the live site results are used to develop better test cases and products.
Live site tests are performed in locations with different weather conditions: Lund in Sweden, Skellefteå in Sweden, and Dubai in United Arab Emirates. The table below indicates the temperature range for the test locations.
Live site | IEC climate zone | Temperature range | Weather conditions given extra attention |
Dubai | Warm damp | 15 °C to 50 °C | High temperatures, corrosion, material deterioration |
Lund | Warm temperate | -15 °C to 35 °C | Condensation, ice or snow |
Skellefteå | Cold temperate | -35 °C to 30 °C | Cold temperatures, ice or snow |

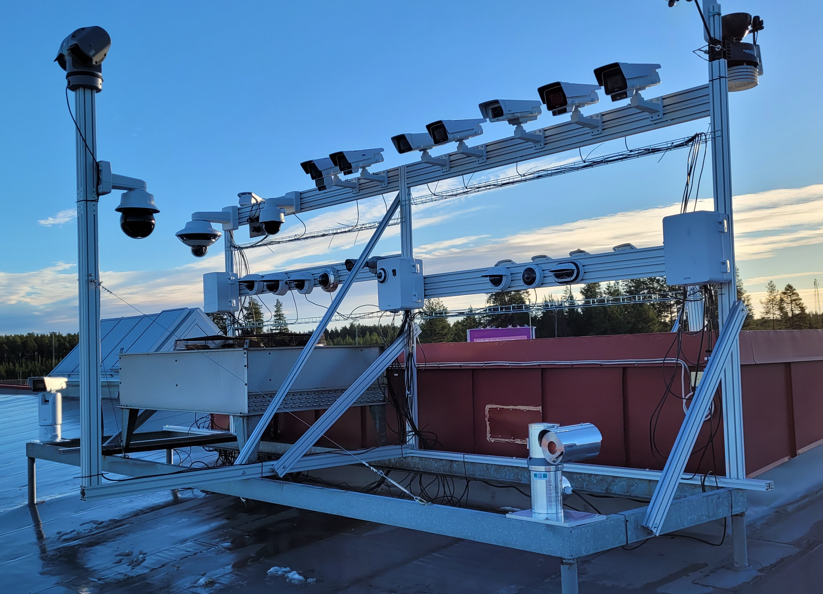
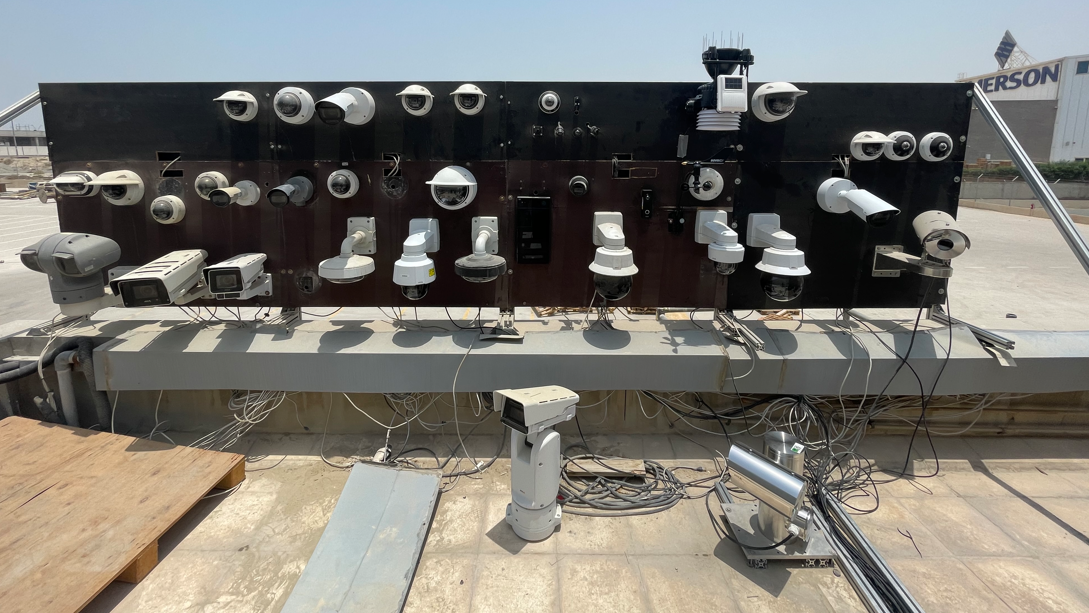
Body worn camera testing
Body worn cameras are part of Axis portfolio and it requires a different testing method. This is because body worn cameras are worn and used in interactive situations and are very mobile. Axis engineers use small shocks, extreme shocks, temperature variation, and a free fall test with 2 metres drop, to check the product’s general robustness and impact resistance.
These tests help to evaluate how the product reacts to quick change in temperature when moved from outdoors to indoors, drops on the ground and other bumps that could occur during usage, abrasion and dust resistance when worn, battery performance, and lifespan.
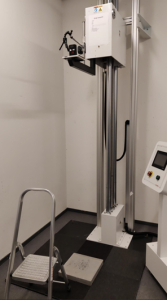
Quality tests during production
A product must be completely and fully operational, with all its intended capabilities at launch, and always with complete documentation for partners and end-customers. To maintain quality assurance, all Axis products are tested thoroughly during production and materials are carefully selected.
Production
A manufacturer working for Axis must apply quality control at all stages of the production process. The quality assurance covers components, tools, management, selection and training of staff, and also the finished products, the packaging of the products, among other things. The finished product must conform to the product design specifications in all aspects.
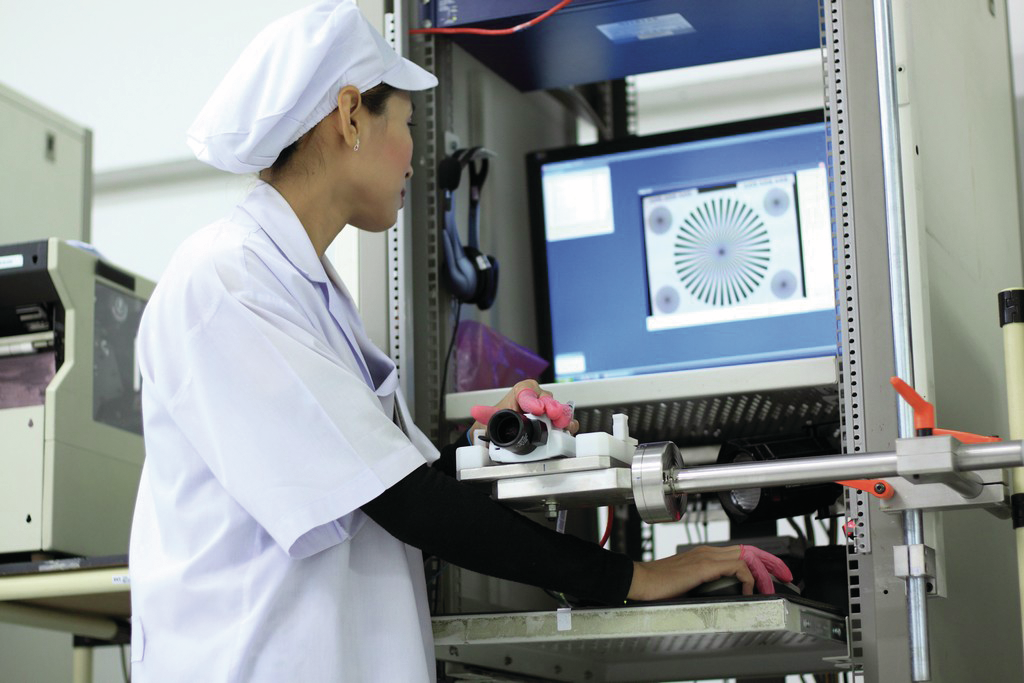
At all Axis manufacturing sites, quality control starts as soon as components arrive. Individual components are checked and measured. Most components, including all critical components, such as image sensors, lenses, product-specific chips and all mechanics, are sourced by Axis to maintain quality assurance throughout the supply chain. Generic components are sourced by Axis-contracted manufacturers. Once the components have been checked, electronics are surface-mounted using state-of-the-art manufacturing methods. To ensure that no error goes undetected, automated and manual testing, including optical, visual and x-ray inspection, are used. PCB assemblies are tested electrically before being approved for the next step, which is box build in a classified clean room. For Axis cameras, a proprietary system of active alignment is used to perfectly align the sensor and lens. Once the box build is completed, a battery of functional tests is performed. Every single unit is tested. Some testing is automated, but every unit is also approved by a trained operator.
In the following step, every single product passes through an Axis Configuration and Logistics Centers (CLC), at various locations around the world. Quality control procedures start as soon as the products arrive. When a customer places an order, the products are picked, configured and once again subjected to a number of tests, similar to the ones during manufacturing, before they are packed. A dedicated tester is responsible for each product.
Materials
The materials chosen in an Axis product are carefully selected to meet up with all the requirements. Axis often uses recycled plastics which helps to reduce environmental footprint and are in close contact with the material suppliers.
Axis products’ windows are made of polycarbonate (PC) and glass and the domes are made of polycarbonate (PC). PC is chosen over the more commonly used polymethyl methacrylate (PMMA). PMMA is more fragile, whereas PC has excellent impact resistance and very good optical properties. The PC grades used in Axis products are of the highest quality, from the top industry material suppliers. It is used in places where impacts and collisions are common, such as police shields, ice hockey rinks and jet fighter canopies. In an Axis product, a window made of plastic will normally only be marked when it is hit, it will not crack or shatter, thanks to its PC material and vigorous IK-testing.
For cameras’ windows and domes, Axis uses PC materials that are hard-coated for better UV and abrasion performance. For non-transparent covers, PC alloys and other materials are used to enhance the ultraviolet (UV) resistance even further.
Axis products are made from materials with very low and compatible thermal expansion coefficients, to minimize focus variations due to temperature variations. This minimizes the effect of temperature on the size of lenses, lens holders and sensor holders, thus avoiding movement of the lens and enhancing maintenance of high image quality.